La mise en pratique
Après la théorie vient la mise en pratique ... y'a plus qu'à comme dirait l'autre
.
Je suis allé chercher mes pièces réalisées par Daniel Winter (alias "Le Chaman" d'Est-Motorcycles à Manzat) les 18 et 19 Décembre 2009 ... un excellent moment que je n'oublierai jamais !
Est-Motorcycles :
Daniel étant un professionnel (comme on n'en fait plus) vivant de sa passion et de ses préparations, par respect pour son travail, je ne divulguerai en aucun cas ici le fruit de ses recherches.
Pour toute question sur le vilebrequin, le piston, la chemise ou l'arbre à cames, vous pouvez le contacter
ici.
Pour ce qui n'engage que mes travaux, les rubriques suivantes seront complétées au fur et à mesure de l'avancée des travaux (avec
en gras ce qui vient d'être mis à jour).
La culasse
La culasse est d'abord micro-billée.
J'ai prévu de remplacer les guides de soupapes et les soupapes par du neuf et de préparer les conduits.
Les pièces neuves :
Pour rappel de la page précédente (La théorie appliquée au moteur de la 500 SR), j'ai choisi d'usiner mes sièges avec les angles suivant :
* Angle de portée de soupape = 45°
* Angle de raccordement avec le conduit interne = 60°
* Angle de raccordement avec la chambre de combustion = 30°
* Largeur de portée siège/soupape = 1,3 à 1,5 mm
Je me suis donc payé l'outillage manuel de rectification des sièges

.
Il est constitué :
- d'une fraise de 30° pour le raccordement siège/conduit interne
- d'une fraise combinée de 45° pour la portée de soupape et de 60° pour le raccordement siège/chambre de combustion
- d'un centreur pilote diamètre 8,00 mm
- d'une poignée en T
Cet outillage me servira également pour les 4 culasses de Ducati (ce n'est pas un V4, mais j'ai un jeu de culasses grosses soupapes de rechange).
A moins d'avoir des guides de soupapes en parfait état (absence d'usure), le remplacement de ces guides est impératif avant la rectification des sièges (on le voit bien sur la culasse de ducati : le guide de la soupape d'échappement a 0,5 mm de jeu).
L'outillage de rectification des sièges :
******************************************
La première étape est le remplacement des guides des soupapes. Pour celà, j'ai réalisé un chasse-guide en laiton. Il servira aussi (et surtout) pour la remise en place des nouveaux guides. Son diamètre correspond à celui des nouveaux guides (il aura donc du jeu dans les anciens guides).
Le chasse-guide :
La culasse passe ensuite au four à 120°C pendant 45 minutes minimum. Les anciens guides sont extraits avec le chasse-guide. Ça va tout seul

.
Puis il faut usiner les nouveaux guides au diamètre extérieur des anciens guides. Je remonterai des guides en bronze à la place de ceux d'origine (qui sont en acier ou en fonte).
J'augmente systématiquement de diamètre extérieur du guide (emmanchement dans la culasse) de 0,02 mm pour compenser les micro-arrachements lors de l'extraction de l'ancien guide (même si la cullase est montée en température).
La mesure précise du diamètre extérieur des anciens guides :
L'étape suivante est une étape clé (à mon avis).
La coaxialité entre le diamètre extérieur du guide (emmanchement dans la culasse) et le diamètre intérieur (guidage de la soupape) est extrêmement importante : l'écart de coaxialité devra être rattrapé par l'usinage des portées du siège. Plus il y aura d'écart, plus il faudra enlever de matière sur le siège.
Je préfère donc soigner cette coaxialité au départ pour éviter de faire des copeaux (en plus avec des fraises manuelles, ... je sais je suis fainéant

).
Donc pour limiter cet écart lors de l'usinage du diamètre extérieur, il faut se guider sur le diamètre intérieur. De plus, pour supprimer le défaut de coaxialité du mandrin, il faudra usiner le diamètre intérieur sans démonter le support.
Ce n'est pas évident à expliquer, des photos seront plus parlantes

.
Le montage d'usinage des nouveaux guides de soupape terminé :
Une barre acier est serrée dans le mandrin, puis usinée au diamètre intérieur des nouveaux guides avec un jeu minimum (il doivent se monter glissant juste). Pour parfaire la coaxialité, l'extrémité du montage est guidée par la contre-pointe.
Avec ce montage, le défaut de coaxialité sera minime : l'axe fictif qui passe par le diamètre intérieur du guide et l'axe fictif qui passe par le diamètre extérieur seront identiques (à quelques microns prêts).
A ce stade, le montage n'est plus démonté du mandrin avant d'avoir terminé les 2 guides, et après ce sera poubelle.
L'usinage du diamètre extérieur des nouveaux guides :
Le nouveau guide est monté (légèrement serré sur le montage), bloqué par l'écrou, guidé par la contre-pointe et usiné au diamètre extérieur de l'ancien guide +0,02 mm.
Là, c'est nickel

.
Le remontage des guides neufs se fait à chaud (culasse rechauffée à 120°C au four) et avec l'outil qui va bien.
Les nouveaux guides montés :
Ensuite, les guides sont alésés au moyen d'alésoirs à main. La finition est réalisée avec un alésoir expansible pour obtenir un jeu guide / tige de soupape de 0,03 mm à l'admission et 0,04 mm à l'échappement.
L'alésage des nouveaux guides de soupape :
Les soupapes sont mises en place avec un jeu impeccable.
Les soupapes en place :
Il reste maintenant à fraiser les sièges de soupape pour que la portée soit parfaite. Avec le montage d'usinage, le défaut devrait être très minime. Seuls les angles seront à travailler.
L'objectif est d'avoir des portées comme sur le schéma.
C'est un jeu de patience, il faut y aller doucement et contrôler les portées au bleu pour s'approcher de l'objectif.
Le montage pour l'usinage des guides était parfait, je n'avais aucun défaut de coaxialité

.
L'usinage des sièges :
Ma technique pour la vérification finale des portées de soupape et la suivante : je passe un coup de marqueur noir sur les soupapes et je les applique sur leurs sièges respectifs avec une rotation.
La portée correspond au marqueur qui a disparu. Je trouve cette méthode plus facilement lisible qu'au bleu.
Le résultat final est parfait (bonne largeur de la portée et bon centrage sur la soupape)

.
La vérification finale des portées de soupape :
Il me reste la finition des conduits (j'avais fait les ébauches quand les guides étaient démontés, mais je n'ai pas fait de photos) et le polissage de la chambre de combustion. Et pour terminer, une mise en peinture et le remontage des soupapes avec leurs ressorts neufs. Mon objectif est de remonter la culasse pour fin Août (de cette année

) ... c'est-à-dire 2019).
La distribution
L'arbre à came (réalisé par Daniel Winter) est une très belle pièce !
Je prévoie uniquement de modifier le calage ... J'en parlerai le moment venu.
Le piston
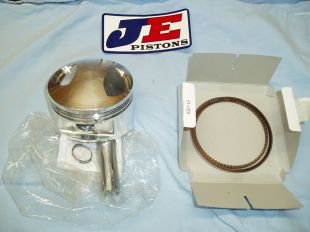
La première étape est de trouver un piston en diamètre 90 mm de bonne qualité et pas trop "racing" (c'est à dire pas de jupe ultra-courte, ni guidages latéraux minimalistes).
En 2005, mon choix s'était porté sur un piston JE forgé (essentiellement pour son niveau de qualité et sa conception adaptée à une utilisation routière).
Maintenant, après réflexion, ce piston comprime à 11:1 théorique avec la course d'origine ... avec une longue course, ce sera beaucoup trop !
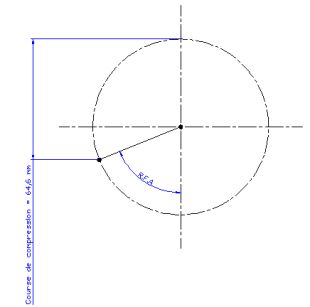
Même en corrigeant ce taux théorique du R.F.A (Retard de Fermeture d'Admission ... souvenez-vous du diagramme d'Otto corrigé, on est proche de la pression atmosphérique à ce moment), le taux de compression effectif (ou taux de compression réel) restera beaucoup trop important pour l'utilisation prévue.
Un rapide calcul nous donne :
Taux de compression = (Cylindrée / Volume chambre de compression) + 1
Comme le piston JE est fortement bombé, celà revient à réduire le volume de la chambre de combustion.
En le montant tel quel, on arrive à un taux de compression théorique de 13:1 !!!!!!
Je me suis donc orienté vers d'autres solutions que ce piston JE.
J'aimais bien celui-ci

... mais un peu trop racing !
En fait, c'est un piston de Renault F1, je l'ai mis là juste pour le fun

.
Plus sérieusement, j'ai opté pour le piston conçu spécialement (toujours par Daniel Winter) pour le longue course. Il est en diamètre 90 mm.
Je ferai uniquement un contrôle du taux de compression par mesure de la chambre de combustion.
La nouvelle chemise du cylindre
Après avoir longuement réfléchi (oui, ça m'arrive des fois

), la solution piston de diamètre 90 mm dans la chemise d'origine ne me plait pas du tout,
car l'épaisseur de la chemise ne serait que de 1,5 mm sur sa partie basse (celle qui n'est plus emmanchée dans le cylindre alu.)
Dans ce cas, même malgré une parfaite co-axialité lors du ré-alésage à 90 mm, les dilatations ne seraient pas homogènes dans cette partie, ce qui engendreraient des usures prématurées et des remontées d'huile.
J'ai donc choisi de remplacer la chemise d'origine par une chemise de diamètre extérieur 96 mm
sur toute sa hauteur, ce qui donne une épaisseur de toile de 3 mm qui est identique au montage d'origine.
L'inconvénient de ce montage est qu'il faut réaléser le cylindre pour monter la chemise plus épaisse, et qu'il faut aussi ré-aléser les carters moteur au diamètre 96 mm.
Et surtout ne me parler pas de meuler les carters à la dremel sous prétexte que le cylindre est déjà centré par 2 pions et que ce centrage de la chemise ne sert à rien

!
Déjà, il sert à plaquer le joint torique d'embase du cylindre et puis, il évitera à la chemise d'encaisser de trop grosses contraintes sur sa partie basse (surtout avec une bielle courte) ... enfin, tout ça sera développé dans la rubrique "Les carters moteur".
La première étape est de sortir la chemise existante.
Pour celà, il suffit de mettre le cylindre au four (froid), de règler la chauffe à 140°C, et de laisser faire ... la chemise vient toute seule.
Si vous êtes vivez seul, il n'y a qu'à attendre. Sinon, il est prudent de prévenir votre entourage ... ça peut surprendre de faire cuire un morceau de métal, et l'odeur n'est pas forcément agréable pour tout le monde

.
La chemise sortie du cylindre :
Voilà le cylindre prêt pour le réalésage et le montage de la nouvelle chemise ... tout ça a été réalisé par Daniel Winter.
******************************************
Maintenant que la nouvelle chemise est en place dans le cylindre, et que les carters moteurs ont été usinés, il reste la partie basse de la chemise à ajuster par rapport au passage du vilebrequin, de la bielle et du piston (comme ça avait été convenu avec Dan).
Je me fixe un jeu mini de 2 mm entre le bas de la chemise et le vilebrequin. Les usinages seront faits à la fraiseuse.
Tout d'abord, comme la chemise fonte est très fragile et que je vais travailler en son extrémité, des montages pour contenir les efforts d'usinage sont réalisés. Ce sont en fait des bagues (intérieure et extérieure) qui vont maintenir l'extrémité de la chemise en place.
Bien sûr, il n'y a pas de jeu pour que les bagues soient efficaces.
Les montages :
En fait la base de la chemise doit être d'un diamètre de 153 mm (diamètre des masses du vilebrequin + 2 mm de jeu au rayon). Comme je n'ai pas de fraise de ce diamètre précis, il faut calculer l'angle d'inclinaison pour que la fraise de 120 mm fasse une développante de cercle qui corresponde au diamètre 153 mm ...
je ne suis pas sûr d'être clair là

.
Avec une photo, ce sera limpide :
Puis la longueur de la chemise est terminée. En fait, je l'ajuste pour qu'elle soit au niveau de la jupe du piston lorsqu'il est au P.M.B.
Si elle est trop courte, le piston ne sera pas suffisamment guidé. Si elle est trop longue, elle risque de toucher les masses du vilebrequin et surtout pénalisera la bonne lubrification du piston.
La finition de la hauteur de la chemise :
Le montage pour vérifier : 1,6 mm de jeu sans le joint ... pas mal non

?
Il reste le passage de la bielle à vérifier ...
Là, c'est trop juste. Ça passe, mais à quelques dixièmes prêts.
Ce n'est pas grave, ça se corrige très bien.
En fait, il faut juste faire une échancrure de la largeur de la bielle + 2 mm et avec l'angle d'attaque de la bielle à l'endroit où ça touche presque.
C'est reparti pour une séance de fraisage :
Puis un dernier montage cylindre / carters :
Et enfin pour finir avec la chemise, une vérification de la cinématique : c'est nickel tout ça ... il va être bien né ce moulin

!
Le cylindre
D'abord, il y a cette question du renforcement du cylindre. Le cylindre encaisse tous les efforts lors des explosions car il n'y a pas de liaisons directes entre la culasse et les carters moteur :
c'est le cylindre qui travaille en traction. De plus, cette résistance est affaiblie par le ré-alésage du diamètre intérieur du cylindre pour passer la nouvelle chemise (plus forte en diamètre extérieur). Le taux
de compression augmente également la contrainte.
En résumé, il y aura plus de contraintes et moins de résistance du cylindre

.
Je pars donc l'ajout de 3 tirants (je ne fais que reproduire ce qui est très bien expliqué dans le site de
Nico).
La seule variante est que j'utilise des têtes fraisées pour une question de résistance de l'embase du cylindre.
La première étape consiste à percer le cylindre. Je me suis servi d'une vis de M10x125 percée au centre comme canon de perçage. C'est à mon avis primordial si l'on ne veut
pas que le foret dévie.
Puis c'est au tour des lamages.
Il faut ensuite percer les 3 goujons, puis les tarauder. Pour ne pas trop les affaiblir, je les ai percés sur 10 mm et taraudés sur 8 mm (taraud à fond plat).
Attention, un taraud est fragile !! Surtout quand on vient en butée au fond du trou (j'en ai cassé 1 !)
Les étapes du renfort du cylindre :
Je me suis posé la question sur la matière des tirants (en inox ou en acier ?).
Tableau de synthèse des coefficients de dilatation linéaire :
|
Coefficient de dilatation (α) |
Aluminium |
2,33.10-5.K-1 |
Acier |
1,22.10-5.K-1 |
Inox 304 (A2) |
1,60.10-5.K-1 |
Inox 316 (A4) |
1,65.10-5.K-1 |
Tableau comparatif des dilatations en fonction des matériaux :
|
Longueur à 20° C (mm) |
Longueur à 150° C (mm) |
Δ (mm) |
Cylindre aluminium |
75 |
75,23 (égal à 75+75x2,33x(150-20)/100000) |
0,23 |
Tirant acier de renfort cylindre |
80 |
80,13 (égal à 80+80x1,22x(150-20)/100000) |
0,13 |
Tirant Inox (304) de renfort cylindre |
80 |
80,17 (égal à 80+80x1,60x(150-20)/100000) |
0,17 |
Nota : la température moyenne du cylindre prise en compte est la plus défavorable : 150
°C (elle varie en moyenne de 120 à 150
°C).
Pour les puristes, le coefficient de dilatation linéaire est extrapolé car il n'est valable que jusqu'à 100
°C.
Les longueurs prises en compte sont les longueurs libres sans contraintes (par exemple, la hauteur du cylindre est celle du plan de joint de culasse à la face d'appui des écrous de fixation du cylindre au bloc moteur).
L'écart de dilatation libre entre le cylindre et les tirants acier est de 0,1 mm, elle est de 0,06 mm pour les tirants inox. Au final, je choisi des tirants inox essentiellement pour la résisitance à l'oxydation.
Il y aura donc 0,06 mm d'écart de dilatation entre le cylindre et les tirants qu'il faudra compenser à froid.
Pour compenser l'écart de dilatation, les tirants sont serrer au couple de 2 Nm à 20°C.
Le seul inconvénient de ce montage est que les renforts ne jouent leur rôle qu'une fois le moteur chaud (cylindre dilaté). Il ne faudra donc pas "tirer" dans le moteur tant que celui-ci n'est pas en température, ce que tout le monde fait ...
Les usinages du cylindre étant terminés, il passe en peinture après avoir été microbillé.
Le cylindre passe à la peinture haute température.
Après 2 jours de séchage à température ambiante, le cylindre passe au four (montée en température jusqu'à 150
°C, par palier de 50
°C).
Une précaution hyper importante est de mettre le cylindre en appui
sur la chemise (au moyen d'une grosse rondelle métallique) pour éviter
tout mouvement de la chemise par rapport au cylindre.
Nota : la rondelle d'appui sur la chemise n'est pas visible sur la photo.
Puis, les renforts de cylindre sont montés (collées à la loctite freinfilet fort).
Le cylindre terminé :
Les carters moteur
1) L'usinage pour le passage de la nouvelle chemise :
Bon, on va attaquer l'usinage des carters (pour laisser passer la nouvelle chemise).
Tout d'abord, il faut mesurer précisément le diamètre de la nouvelle chemise :
Pour contrer la poussée du piston du L.C.B.C, il faut impérativement que la chemise soit correctement maintenue par le carter en partie basse,
mais pas trop car elle doit aussi pouvoir se dilater en longueur (avec le cylindre, car elle est bloquée par la culasse sur la partie haute du cylindre).
Je vais donc mettre 0,00 mm à 0,01 mm de jeu (pas trop facile à réaliser

).
Autre point important, je veux conserver la possibilité de remonter un cylindre d'origine sur ces carters, toujours en maintenant la partie basse de la chemise
(car on pourrait remonter le cylindre uniquement centré avec les 2 pions sans maintenir la chemise dans le carter, mais ça ne me plait pas).
Tout ça pour dire qu'un petit lamage sera effectué pour monter soit une simple rondelle avec la nouvelle chemise, soit une bague épaulée pour un cylindre d'origine ... Ça va, vous suivez

?
Un petit schéma sera plus parlant :
(Les 2 versions de bagues (simple rondelle et bague épaulée) sont en rouge sur les schémas).
Bon, on peut attaquer les usinages (en images) ...
L'opération la plus important (qui donnera toute la précision) : le montage et le réglage de la fraiseuse.
(Petit rappel, les carters sont montés avec 2 pions de centrage neufs).
D'abord, il faut les brider (sans les déformer) sur la table de la fraiseuse. Ensuite, la tête est inclinée pour que l'axe outil soit parfaitement perpendiculaire à la surface d'appui du cylindre.
Cette opération est effectuée au comparateur.
Ensuite, l'axe outil est parfaitement réglé coaxial à l'axe fictif défini par les 2 pions de centrage existants (au moyen d'un pépita).
Pour finir, la tête à aléser est montée ... c'est prêt !
Voilà ce que ça donne :
Il n'y a plus qu'à réaliser le bon diamètre et l'épaulement :
Les carters terminés (avec la rondelle) :
P-S : la bague épaulée pour le cylindre d'origine n'est pas encore réalisée (normalement j'ai le temps avant de remonter le cylindre d'origine ... enfin j'espère

...).
Bon, maintenant il faut vérifier le bon montage du cylindre. Il sera certainement nécessaire d'ajuster la chemise aux fonderies des carters.
Le cylindre est monté dans les carters (avec les 2 pions de centrage) : c'est juste-juste (aucun jeu), mais ça se monte ! Je suis très satisfait des usinages

!
Il ne se monte pas à fond, mais c'est normal car il faut ajuster le bas de la chemise au vilebrequin.
2) Le contrôle de la co-axialité des alésages des roulements des carters :
L'étape suivante est le contrôle de la coaxialité des alésages des roulements de vilebrequin. Ce critère est tout aussi important que l'alignement du vilebrequin. En effet, ça ne sert à rien d'avoir un alignement
du vilebrequin à 0,02 mm s'il est monté dans des logements qui ont 0,10 mm de défaut de coaxialité

!
Pour ça, 2 bagues parfaitement coaxiales (réalisées au tour sans aucun démontage) sont usinées pour être montées juste glissantes (0,01 mm de jeu) dans chaque carter à la place des roulements.
Toujours sans démontage, un alésage diamètre 20 mm est réalisé pour recevoir un axe rectifié avec 0,01 mm de jeu. Une fois tous ces diamètres réalisés, les bagues sont tronçonnées.
Chaque bague est montée dans chaque alésage de roulement, puis les carters sont assemblés (toujours avec 2 pions de centrage neufs).
Maintenant, si l'axe rectifié se monte glissant juste, la coaxialité est bonne. Si ça force, déjà c'est pas bon signe

... dans ce cas il faut augmenter l'alésage intérieur des bagues centième par centième jusqu'à ce que ça se rentre glissant juste.
Verdict quand l'axe est présenté : ça ne force absolument pas et ça se monte bien glissant, donc les carters sont nickels

!!!
Les gabarits de vérification de la coaxialité des alésages des roulements de vilebrequin :
3) L'usinage pour le passage du vilebrequin :
Avant d'attaquer la mise en peinture des carters, je vais faire un montage à blanc de l'ensemble vilebrequin/piston/cylindre pour être sûr que tout se passe bien.
Pour ça, je remonte les anciens roulements dans les carters.
Mince, je ne m'attendais pas à ça

: le vilebrequin ne passe pas au niveau des récupérateurs d'huile !
Ce sont pourtant des carters de SR (avec des masses de vilebrequin de plus grand diamètre). Il ne faut normalement ré-usiner que les carters d'XT ... il y a un truc qui m'échappe là

.
Après quelques mesures, je viens d'en découvrir la cause : le diamètre des masses d'un vilebrequin de SR 48T est identique à celui du XT ! En fait, ça se comprend : ça aurait fait trop d'inertie pour les 27 cv.
- Diamètre extérieur des masses du vilebrequin 500 XT : 142 mm
- Diamètre extérieur des masses du vilebrequin 500 SR (2J4) : 149 mm
- Diamètre extérieur des masses du vilebrequin 500 SR (48T) : 142 mm
Comme c'est une base de vilebrequin de 500 SR 2J4 qui a servi à la construction du longue course, il faut donc ré-usiner les carters pour mettre 2 mm de jeu entre le diamètre des masses et le récupérateur d'huile.
Le premier demi-carter est bridé (sans le déformer) sur la table de la fraiseuse, puis la tête d'usinage est centrée dans l'alésage du roulement.
Je n'ai pas voulu démonter les roulements car cette opération ne nécessite pas une grande précision et surtout que je n'ai pas envie de perdre du temps à remonter/démonter les roulements à chaque remontage à blanc.
Le centrage est quand même fait au pepitas, à quelques centièmes près

...
Le demi-carter en place et le réglage fraiseuse fait :
Là, je suis obligé de "bricoler" ma tête à aléser qui ne me permet normalement pas d'aléser à plus de 100 mm. Ce n'est pas très esthétique, mais ça fonctionne en prenant des petites passes.
Le demi-carter usiné :
Juste pour voir, le demi-carter pas encore usiné est positionné sur celui usiné. Ça fait quand même une différence

!
La différence pièce usinée (photo de droite, pièce à gauche) et non usinée (photo de droite, pièce à droite) :
Puis, c'est au tour du second demi-carter.
L'usinage du second demi-carter et la vérification (il y a 1,8 mm de jeu entre le vilebrequin et les récupérateurs d'huile) :
Bon, ben il n'y a plus qu'à passer les carters en peinture. Les vieux roulements sont re-démontés.
Les carters prêts pour la mise en peinture :
Au printemps 2012, les carters passent en peinture. J'ai utilisé le kit complet gris de chez Restom. C'est pas donné, mais la qualité est là.
Les carters terminés :
Le vilebrequin
Voici la pièce maîtresse de cette préparation avec 10 mm course en plus et une bielle courte pour ne pas avoir à caler le cylindre. Les 10 mm sont donc gagnés "en bas" de la course.
C'est vraiment du très beau boulot réalisé par Daniel Winter

!!!
Nous sommes en Novembre 2011, ça fait déjà 2 ans que le vilebrequin attend (bien emballé et huilé) ...
Comme un des critères principal de la fiabilité d'un moteur préparé est la métrologie de l'ensemble mobile, et comme mon carton avec le vilebrequin s'est pas mal balladé, je vais tout vérifier minutieusement.
L'alignement est
LE point clé de la fiabilité et le gage d'un moteur qui ne vibrera pas !
Concernant ma méthode de mesure (il y en a d'autres, mais je fais avec les moyens dont je dispose et qui sont déjà pas mal

), je monte le vilebrequin en mors doux (préalablement usiné au bon diamètre)
par un des 2 tourillons du vilebrequin. C'est en fait mon point "zéro" : le point de rotation de référence est donc là où sera monté un des deux roulements.
Puis, sans mettre la contre-point pour ne pas générer de contrainte, je mesure et repère sur le second tourillon du vilebrequin les points mini et maxi.
Après quelques corrections minimes, le résultat final est excellent :
0,02 mm de défaut d'alignement !
Un dernier contrôle du jeu latéral de la tête de bielle : 0,40 mm. C'est parfait !
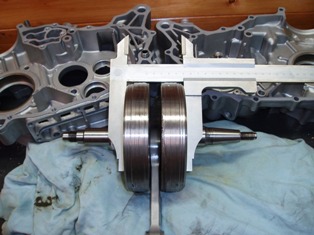
Puis, pour finir, il reste à mesurer la cote extérieur du vilebrequin qui doit être comprise entre 74.94 mm et 75,00 mm selon la revue technique.
La valeur mesurée est de 75,00 mm pour un longement mesuré à 75,26 mm. C'est donc tout bon !
P-S : ça c'est du pied à coulisse non

?
A partir de maintenant, à part moi, interdiction de toucher au vilebrequin !!!
La lubrification
Le moteur étant entièrement montés sur roulements, il n'a pas besoin de pression d'huile, mais de débit, qui va servir à évacuer les calories.
La pompe à huile gros débit (+50%) vient de chez Kedo.
La pompe à huile gros débit :
Il n'y a pas grand chose à faire, si ce n'est qu'il faut bien soigner le montage

!
La pompe à huile montée :
L'échappement
Le tube d'échappement est réalisé en tube inox cintré de diamètre 42,4 mm extérieur et 38,4 mm intérieur.
J'ai beaucoup entendu parler de "torque valve" (qui est en fait un venturi rajouté en sortie de culasse et censé améliorer le couple à bas et moyen régime), mais sans jamais connaitre sa réelle efficacité.
Je vais donc profiter de la construction du tube d'échappement pour tester ce dispositif.
Je réalise au tour une bride inox pour la fixation du tube à la culasse, puis je la fais souder avec un décalage de 6 mm.
Ce décalage permettra de monter soit un venturi, soit une bague simple sans changer la position du tube par rapport au moteur et au cadre.
Je me suis posé pas mal de questions sur les dimensions du venturi. Voilà ce que j'en ai retenu :
1) La théorie :
Synthèse des règles de calculs des venturis :
|
Valeur théorique idéale |
Angle d'ouverture convergent |
21° |
Longueur du col |
Diamètre du col |
Angle d'ouverture divergent |
7° à 15° (idéal proche de 7°) |
Ratio diamètres (col / entrée) |
0,6 |
2) Le venturi Kedo :
L'inconvénient majeur pour implanter un venturi est le manque de place en longueur (à cause du coude du tube d'échappement).
Il faut donc trouver un compromis entre la théorie et la pratique.
Voici les valeurs de celui vendu par Kedo.
|
Valeur |
Angle d'ouverture convergent (α) |
31° (idéal 21°) |
Longueur du col |
0,33 x Diamètre du col (idéal 1 x) |
Angle d'ouverture divergent (β) |
23° (idéal proche de 7°) |
Ratio diamètres (col / entrée) |
0,76 (idéal 0,6) |
3) Le venturi "Home made" :
J'ai essayé de me rapprocher du théorique, et j'ai aussi augmenté le diamètre du col (à 32 mm) car le diamètre du col de 30 mm me semblait un peu trop juste par rapport
à la nouvelle cylindrée et au régime moteur qui sera un peu plus élévé.
Après pas mal de simulations (tout est lié : tout changement de valeur impacte les autres valeurs), voici le compromis auquel j'arrive :
|
Valeur |
Angle d'ouverture convergent (α) |
22° (idéal 21°) |
Longueur du col |
0,3 x Diamètre du col (idéal 1 x) |
Angle d'ouverture divergent (β) |
8° (idéal proche de 7°) |
Ratio diamètres (col / entrée) |
0,8 (idéal 0,6) |
Il est plus proche du théorique, mais il n'est pas dit qu'il amène plus que celui de Kedo ou que sans venturi ... à suivre lors des essais moteur.
Voilà le plan exact avec les dimensions qui a servi à réaliser le venturi en laiton :
Le venturi réalisé en laiton :
Et pour finir les différentes parties et configurations possibles : le tube avec sa bride inox soudée, la bague simple montée, le venturi monté :
4) Le silencieux :
Pour le silencieux (enfin, si on peut peut appeler ça un silencieux), je monte un Mégaton version longue (600 mm) et démontable.
Même s'il est neuf, je remplace quand même l'insonorisant, car il est livré juste avec un juste peu de laine d'acier qui ne sert pas à grand chose.
Je profite du démontage pour passer un coup d'antirouille haute-température sur le tube central et l'intérieur du mégaphone (qui sont en acier brut).
Je le remonte avec le plein de laine de céramique (que l'on trouve en kit chez tous les accessoiristes pour une quinzaine d'Euros).
En fonction des essais (et des réactions du voisinage !), je rajouterai un Db Killer dans le cone.
Les étapes de l'amélioration du Mégaton :
La boite de vitesse
Il faut prendre soin de bien caler les arbres (avec suffisamment de jeu, mais pas trop ...

).
En fait, il faut que les dentures soient bien en face les unes par rapport aux autres.
Ma méthode est de tout monter à blanc (sans aucune rondelle), de mesurer les jeux pour chacun des arbres dans leurs positions extrêmes, puis des faire des rondelles de calage adéquates pour que les engrenages soient bien face à face.
Le montage à blanc sans rondelles de calage pour les mesures :
Puis les rondelles de calage sont mises en place et le vilebrequin est remonté. Je rappelle au passage qu'on en frappe jamais sur un vilebrequin (qui a été aligné au centième) pour le remonter

!!!!!
Pour ma part, j'utilise des bagues de différentes longueur en me servant du filetage d'extrémité pour mettre en place le vilebrequin dans son roulement.
Le remontage du vilebrequin :
Il n'y a plus qu'à étancher, et à refermer !
La transmission
Devant avoir un peu plus de couple avec la préparation moteur, il me faut modifier le rapport de transmission.
D'abord, je passe sur une chaine de 520 (c'est celle d'origine sur la XT). Je trouve la 530 (celle d'origine sur la SR 2J4) inutile pour la puissance d'un mono. A l'opposé, la 428 d'origine de la SR 48T fait faiblarde.
Ci-dessous les différentes combinaisons possibles :
|
Pignon |
Couronne |
Largeur de chaine |
Démultiplication |
Pourcentage de différence par rapport à l'origine |
Origine 48T |
20 |
55 |
428 |
2,75 |
- |
Origine 2J4 |
16 |
42 |
530 |
2,63 |
5 % |
Origine 500 XT |
16 |
42 |
520 |
2,62 |
5 % |
Possibilité 1 |
16 |
41 |
520 |
2,56 |
7 % |
Possibilité 2 |
17 |
42 |
520 |
2,47 |
10 % |
Possibilité 3 |
17 |
41 |
520 |
2,41 |
12 % |
Possibilité 4 |
17 |
40 |
520 |
2,35 |
14 % |
Au final, je retiens le 17 x 41, car la couronne en 40 est limite en diamètre avec le risque que le sommet des maillons de la chaine touche le moyeu.
Ça risque de tirer encore trop court, mais je verrai bien.